We introduce part of the manufacturing process of the Etsuro series with video.
Cooperative relationship between
Dai-Ichi Shoji and Excel Sound
Establishment period
Dai-Ichi Shoji Co., Ltd. was founded in Yokohama in 1952 and has exported Japanese industrial products to various parts of the world for the last 67 years.
As the system changed from the Tokugawa Shogunate to the Meiji New Government, Yokohama Port began to take steps toward becoming a modern state, forming its cityscape, and at the same time it opened as the international trade port adjacent to the capital of Tokyo to become the accumulation area for a variety of products from all over the world and Japan.
Now that it has operated in Yokohama for over 150 years, Japanese people living in the area have become familiar with foreign cultures due to involvement through work and life.
-
Raw Silk Loading at No.4 Quay in the Port at Yokohama. Raw Silk Loading at No.4 Quay in the Port at Yokohama.
-
Hikawamaru Hikawamaru
-
Yokohama China Town Landscape Yokohama China Town Landscape
-
Mt. Fuji & The land mark tower are desired ,Yokohama port at dusk Mt. Fuji & The land mark tower are desired ,Yokohama port at dusk
-
A lot of gantry cranes are lining up A lot of gantry cranes are lining up
-
Bonded goods burick warehouse Bonded goods burick warehouse
https://etsurojapan.com/concept#sigProId59f07047fe
Achievement of DSK & Excel Sound
The founder of Dai-Ichi Shoji opened access to a home that did not suffer damage during the Second World War to create an office and established a trading company with fellow alumni specializing in exporting cotton products. Later on, in the late 1960s, Dai-Ichi Shoji developed a range of compact electronic measuring instruments with partner companies to export them to various areas around the world.
Dai-Ichi Shoji began exporting OEM phono cartridges around the same time. In the 1980s, Dai-Ichi Shoji also imported and sold Obelisk, Magnepan (speakers), Oracle (turntables) and Conrad Johnson (amplifiers) from the United States, and opened a showroom to enable people to listen to the products at Tokyo Shimbashi. Established in 1970, Excel Sound commenced the production of its own branded cartridge. From 1975 to the 1980s, Excel Sound manufactured OEM products for Japanese audio manufacturers (Pioneer, Sansui, Trio, and Sanyo) as well as overseas audio manufacturers. At its peak, the production volume of MM cartridges was 50,000 pieces per month.
Once the production of CDs commenced in 1982, the production of cartridges reduced, and currently mainly OEM MC and MM cartridges are being produced. Dai-Ichi Shoji has been exporting Excel brand products and OEM items overseas since the establishment of Excel Sound, and this cooperative relationship has continued until the present.
-
Excel Sound President Masao Okada Excel Sound President Masao Okada
-
UP Shelf: B&K Type 2305 Level Recorder,Lower Shelf: L/P Balance separation Recorder for AQL UP Shelf: B&K Type 2305 Level Recorder,Lower Shelf: L/P Balance separation Recorder for AQL
-
Univolt Degital Multi tester Univolt Degital Multi tester
-
Uni Sound Speakers Uni Sound Speakers
https://etsurojapan.com/concept#sigProId0199905d49
Components, process and quality control
In 2016, Excel Sound and Dai-Ichi Shoji jointly planned and developed the Etsuro series high-end MC cartridge. Excel Sound designed each component (stylus tip, cantilever, housing, rubber damper, coil wire, core, base, connection terminal, etc.) comprising the main part of the cartridge series. Using our own tooling, the components are produced by each specialized material processing company. The materials of the main components are made only in Japan and are carefully selected. The winding process of the MC coils and the assembly of each component are processed under strict quality control and are handmade one by one by Excel Sound’s skilled craftsmen.
https://etsurojapan.com/concept#sigProIdcaf840dc16
Japanese Traditional Crafting Techniques and Etsuro Series
The gold leaf or lacquer coating applied to the surface of the housing has been finished in a way that expresses the tradition of Japanese culture that has been passed down to the present from ancient times in Japan. These crafting techniques are used all over Japan for shrines and temple architectures, art objects, and furniture, and have been carried out from over 1,000 years ago to the present.
The Etsuro series is a masterpiece created as a result of the combination of Excel Sound’s technology and Japanese ancient traditional crafting technology that has sought to revive the memories of sounds cut in record grooves.
It is our passion and mission to deliver the Etsuro Series products to analog music enthusiasts around the world.
https://etsurojapan.com/concept#sigProId97d6a1bce4
CRAFTMANSHIP of URUSHI SAKAMOTO
With the cooperation of long-established Urushi Coating manufacturer Urushi Sakamoto, we have succeeded in producing a Japanese aesthetic cartridge with a variety of unique characteristics.
Each cartridge body has been handmade and coated by the skilled craftsmen of Urushi Sakamoto.
https://etsurojapan.com/concept#sigProIda0a1fe7c65
What urushi is and its characteristics:
As china refers to porcelain, japan is also an expression for lacquerware. That is how superb the quality of Japanese lacquerware is, and it is known and prized around the world.
Urushi is made from tree sap collected by cutting the surface of the tree. This whitish rubber-like sap is collected and can then have color pigments added to repeatedly refine it until it is finally used as the coating.
Once the coating is applied and dried through various technical processes, urushi has superb adhesion and strength. The higher the humidity, the better the hardening and the easier it is to process. One of the reasons why traditional urushi craft grew in Japan was due to Japan’s humid climate throughout the year.
The coating created with urushi is distinctly rigid and is said to have even stronger performance in comparison to today’s general chemical coatings . Urushi is also known for its resistance to alkalis, acids, alcohol and water, as well as its thermal insulation and antiseptic performance. Because urushi has these superior strengths, as well as a distinctively beautiful shine, it was used for many years in Japan for traditional artworks such as lacquerware and musical instruments, as well as for the body armor of the Samurai.
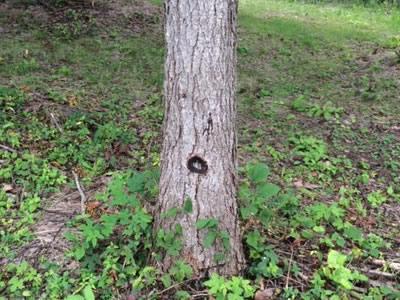
Etsuro Urushi cartridge:
The combination of the A7075 extra super duralmine housing material chosen for the cartridge body, together with the traditional urushi coating applied on the surface, created an ultra-rigid body for a fine but stable cartridge to control unnecessary resonance. Etsuro Urushi Bordeaux and Cobalt have succeeded in utilizing the traditional Japanese techniques from both the perspective of design/aesthetic sense and the sound based on the mechanical characteristics, creating a true piece of artwork.
https://etsurojapan.com/concept#sigProId8d16f81e6c
KINPAKU - TRADITIONAL GOLD FOIL
We have collaborated with one of the most well-known metal leaf developers, Hakuichi Incorporated in Kanazawa prefecture, where 98% of all Japan’s gold foil production takes place.
About Kanazawa gold foil, Kinpaku:
Kanazawa accounts for more than 98% of all gold foil production in Japan. Gold leaf is used in a variety of crafts, such as lacquerware and ceramics, as well as in temples and shrines with high historical value, such as Kinkaku-ji and Nikko Tosho-gu. Gold foil has been developed the most among the 36 types of traditional craft techniques that have been passed down from the time of the first Kaga feudal lord, Toshiie Maeda. Noh and tea ceremonies were frequently held as part of the domain’s cultural incentives, which led to the development of traditional crafts. It is said that the enduring artisan spirit fostered by the climate topography and the Hokuriku region itself is also one of the main factors for the development of gold foil.
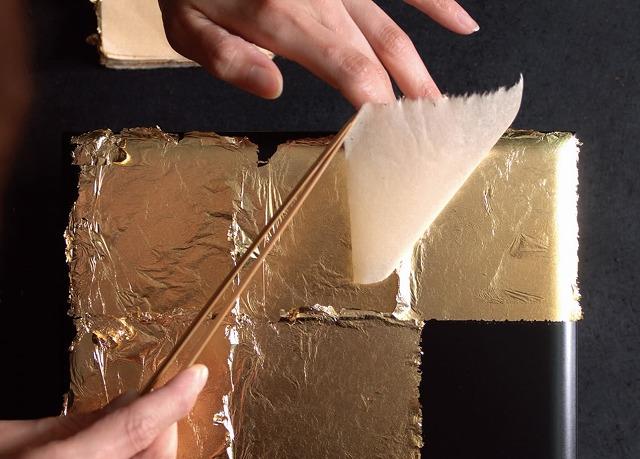
How it is made
Gold leaf is roughly 0.0001 – 0.0002 mm thick.
This is possible with techniques that thin out roughly 2 g (1/2 the weight of a 10-yen coin) of gold into a single sheet that is as thin as possible.
In order to thin out the gold as much as possible, superior craftsmanship as well as the necessary elements are required, including special paper that is said to influence production and a suitable climate for gold leaf production.
Stage1Gold alloy
First, small amounts of silver and bronze are melted and mixed into the gold. These are added to help adjust the tint of the gold, and also because 99.99% pure gold is too soft and difficult to make into gold leaf. The gold, silver, and bronze are placed in a 1300℃ (2372°F) melting pot, and after they have melted, the liquid metal is poured into a mold and formed into a shape. | ![]() |
Stage2Gold Stretching
The alloy is placed into a rolling machine and stretched into a belt-like shape. This is repeated about 20times, until the alloy is about 0.02 – 0.03mm thin. This is then cut into roughly 6cm squares. This square is called koppe. |
![]() |
Stage3Beating and stretching
The koppe is further thinned by beating and stretching it against multiple sheets of paper. When the gold has been stretched out to a 12 cm square, it is called aragane. The aragane is then cut into fourths. After it is stretched out once again, it is called oyju. This is then placed between pieces of finishing paper, and is called uwazumi. At this point, it is roughly 0.003 mm thin. |
![]() |
Stage4Pulling in
From here, the uwazumi is worked from 0.003 mm down to about 0.0001 – 0.0002 mm thick. It is then cut into 12 sheets, and is called coma. The coma is then placed, sheet by sheet, between pieces of gold leaf beating paper. |
![]() |
Stage5Before beating
The gold leaf placed between the beating paper is fixed to this film and is then beaten with a special gold leaf beating machine. Once it has been beaten, the paper is no longer needed, and the leaf is moved to the main paper. It has now been thinned to roughly 0.0001mm.About the paper: This Japanese paper is essential for making gold leaf. The leaf is placed between sheets of the paper, and then the leaf is beaten. The paper is so important that it is said that the paper determines the quality of the gold leaf. Japanese paper can be dipped in egg, acidic fruit juice, or liquid that has been heated by ashes, and it still does not break easily when beating. |
![]() |
Stage6Removal
While checking the quality of the finished gold leaf, each sheet is moved to a hiromono-cho (a pad). Bamboo chopsticks and fossilized shark teeth are used, as they are static-free. Because the gold leaf is only 0.0001mm thick, even the slightest breeze or static electricity could cause it to tear, making this an incredibly delicate job. |
![]() |
Stage7Moving the gold leaf
In the final stage, the gold leaf that has been moved to the hiromono-cho is cut into pieces of the same size. There are four sizes of gold leaf squares: 10.9 cm, 12.7 cm, 15.8 cm, and 21.2 cm. The leaf is cut using a bamboo frame. The cutis plate is held in the left hand, and the gold leaf is moved from the hirimono-cho using bamboo chopsticks. The top and bottom of the gold leaf are then cut, followed by the right and left. The cut leaf is finally placed onto cut paper and is then complete. |
![]() |
Etsuro gold and gold foil
Etsuro Gold is finished with Hon Kinpaku, using 24K pure gold leaf to cover its extra-super duralumin (A7075) body. The 24K gold leaf is carefully applied to this ultra-rigid, high-strength duralumin base, combining exceptional mechanical performance with traditional Japanese craftsmanship. Each piece of gold leaf is meticulously laid onto the precisely machined duralumin body by skilled artisans, creating a luxurious and refined finish.